Die Cut Mylar Bag
A die cut Mylar bag is a high-quality, customizable packaging solution designed for a variety of products, including snacks, supplements, and cosmetics. Crafted from Mylar, a type of polyester film known for its durability and moisture resistance, these bags provide excellent protection and extended shelf life for contents
EXCELLENT Based on 7 reviews More Than Candles2021-12-17Trustindex verifies that the original source of the review is Google. I want to thank ClipnBox for the fabulous work and specially to Adam who has been an amazing support through the developing of my boxes. I am coming back for more!! Happy Holidays to all :) John Li2021-09-10Trustindex verifies that the original source of the review is Google. I am not a reviewer usually but I had an urgent need for custom packaging for my business and I am really surprised and happy with the customer service, turnaround time and the quality of ClipnBox that I am writing this as an appreciation!ย Special thanks to Alex for all the support, Job well done! Custom Jewelry2021-08-03Trustindex verifies that the original source of the review is Google. The company was great to work with. Adam was always very attentive and worked toward delivering what we envisioned. We have not yet launched our brand , but once we do , I will update this review to include pictures. Adam worked with us every step and followed up with emails and calls. If you want to receive a great product and excellent customer service , do not hesitate to work with this company. They are responsible and follow through. Thanks Adam! Malyia Mcnaughton2021-06-22Trustindex verifies that the original source of the review is Google. Great customer service and great quality product! Adam went above and beyond to meet a very quick turnaround and his information was clear and concise. He shipped the boxes with a few samples of a design I had to pivot from as a keep sake which was so unexpected and appreciated.I received the boxes ahead of the very tight delivery date, I don't know how they did it. Very satisfied. I will definitely be using them again for packaging. Comfortable Solutions2021-05-05Trustindex verifies that the original source of the review is Google. Brilliant! No time wasted at all. My order was responded and organized right away. quality of boxes was wonderful. You are my box company . Keep up good things. Jailias Lee2021-04-27Trustindex verifies that the original source of the review is Google. I love this! The quality is good and I am satisfied! The person who helped me was Adam, super responsive and super friendly! I will be buying more from here! I love my new boxes! Gabriel Washington2021-04-20Trustindex verifies that the original source of the review is Google. Very good custom box printing company with exceptional customer service. Our second order from them and they were as professional and prompt as the first time. All boxes I ordered are of good printing quality and durable.Verified by TrustindexTrustindex verified badge is the Universal Symbol of Trust. Only the greatest companies can get the verified badge who has a review score above 4.5, based on customer reviews over the past 12 months. Read more
Our Easy Order Process
Choose from our extensive packaging solutions and personalize them with a variety of options to bring your ideal packaging to life.
After customizing your packaging, simply request a quote, and our packaging specialists will review your submission.
Get expert consultation on your quote to reduce costs, improve efficiency, and minimize environmental impact.
After finalizing the details, weโll handle the entire production and shipping process. Just sit back and wait for your packaging to arrive!
What is a Die Cut Mylar Bag?
A die-cut Mylar bag is a packaging type made from Mylar material, a polyester film. Manufacturers cut these bags into specific shapes to fit particular products. Die-cut Mylar bags remain durable, flexible, and resistant to moisture, making them ideal for packaging food, cosmetics, and other sensitive products.
History of Die Cut Mylar Bags
People have used die-cut Mylar bags for several decades. The first bags appeared in the 1960s. Since then, they have become a staple in the packaging industry, offering various designs, materials, and features to meet different needs and preferences.
Design and Features
Die-cut Mylar bags feature a variety of designs and attributes, including:
Materials
Manufacturers make these bags from high-quality Mylar material, which is durable, flexible, and resistant to moisture.
Shapes and Sizes
Die-cut Mylar bags come in different shapes and sizes, from small, compact bags to large, elaborate designs.
Printing Options:
Users can print a range of designs and logos on die-cut Mylar bags, allowing for customization.
Uses of Die Cut Mylar Bags
People use die-cut Mylar bags for various purposes, including:
Food Packaging:
These bags are ideal for packaging food products such as coffee, tea, and snacks.
Cosmetic Packaging:
They also serve to package cosmetic products like skincare and haircare items.
Benefits of Die Cut Mylar Bags
Die-cut Mylar bags offer several benefits, including:
Convenience
They are easy to use and provide a convenient way to store and transport products.
Portability
Their lightweight nature makes them easy to carry on the go.
Protection
They offer a protective barrier against moisture, air, and light, keeping products fresh and safe.
Types of Die-Cut Mylar Bags
Several types of die-cut Mylar bags are available, including:
Standard
These bags are made from standard materials and come in various sizes.
Custom
Manufacturers produce custom die-cut Mylar bags from custom materials and design them to fit specific needs.
Specialty
Specialty bags offer unique features like waterproofing or UV protection.
How to Choose the Right Die-Cut Mylar Bag
To choose the right die-cut Mylar bag, consider the following factors:
Intended Use
Determine how the bag will be used and choose a material and design that fits that use.
Customization
Decide if you need a custom design or material to meet specific needs.
Budget
Set a budget and select an option that fits within that financial plan.
Choosing the right printing method is essential for creating high-quality custom packaging that represents your brand effectively. We offer three premium printing options to ensure vibrant colors, sharp details, and a professional finish. Whether you need cost-effective digital printing, high-volume offset printing, or striking UV printing for added impact, we have the perfect solution for your packaging needs.
Take your custom boxes to the next level with luxury finishes like embossing, foiling, spot UV, and moreโbecause your brand deserves to stand out!
Premium Lamination Options
Stunning Add-ons
Paper Type | Thickness (Pt) | GSM | Common Uses |
---|---|---|---|
Thin Paper | 4 – 6 pt | 50 – 90 | Newspapers, book pages, inserts |
Text Weight Paper | 8 – 10 pt | 100 – 150 | Flyers, brochures, magazines |
Light Cardstock | 12 – 14 pt | 160 – 220 | Lightweight cartons, greeting cards |
Standard Cardstock | 16 – 18 pt | 230 – 310 | Product boxes, retail packaging |
Heavy Cardstock | 20 – 22 pt | 320 – 400 | Premium rigid boxes, business cards |
Extra Thick Cardstock | 24 – 28 pt | 420 – 600 | Luxury packaging, invitation cards |
Corrugated Board (Single Wall) | 24 – 40 pt | 250 – 600 | Mailer boxes, e-commerce shipping |
Corrugated Board (Double Wall) | 40 – 60 pt | 600 – 900 | Heavy-duty shipping, industrial packaging |
Chipboard (Rigid Box Material) | 30 – 60 pt | 600 – 1200 | Luxury rigid boxes, high-end packaging |
- For lightweight packaging (e.g., product sleeves, paper bags): Choose 12-16 pt.
- For standard product boxes (e.g., cosmetics, small retail items): 16-20 pt works well.
- For premium packaging (e.g., rigid gift boxes, high-end branding): Go for 24 pt and above.
- For shipping & mailers (e.g., e-commerce boxes, subscription packaging): Use corrugated board (24-60 pt).
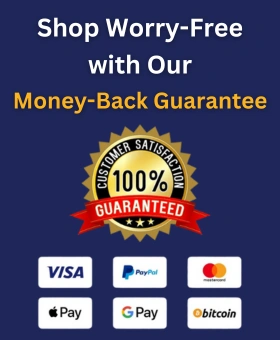